Introduction
Applying advanced surface coating technologies in plastic mold components plays a pivotal role in ensuring longevity and wear resistance. For users seeking high-quality components, understanding the nuances of these coatings is essential. This article delves into the critical surface coating technologies that enhance the performance of plastic mold components.
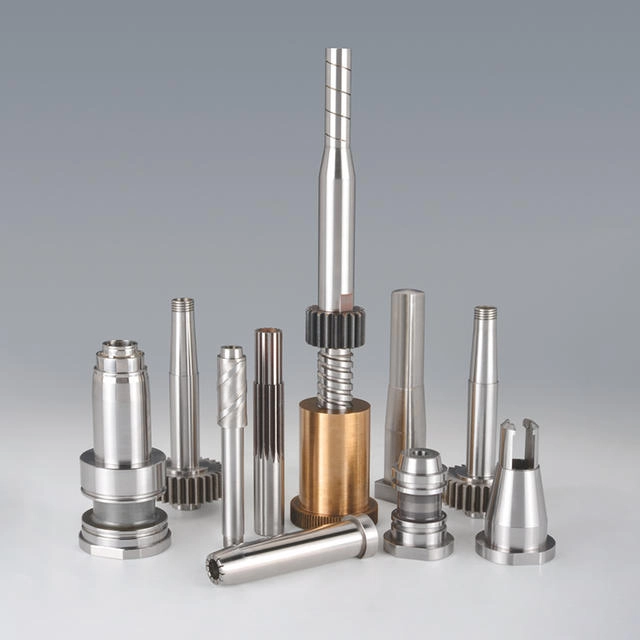
Key Surface Coating Technologies
1.Overview of Common Surface Coating Technologies
Surface coating technologies serve as protective layers, shielding plastic mold components from wear and tear. Several widely adopted coatings include:
2.In-depth Exploration of Specific Technologies
1.PVD (Physical Vapor Deposition) Coatings
PVD coatings, known for their thin film deposition, offer exceptional hardness and resistance to abrasion. This technology is a hallmark in the plastic mold components industry.
2.DLC (Diamond-Like Carbon) Coatings
DLC coatings mimic the properties of natural diamonds, providing hardness and a low friction coefficient. Plastic mold components benefit from reduced wear and increased lifespan with DLC coatings.
3.Nitriding Processes
Nitriding involves diffusing nitrogen into the surface of the mold components, creating a hard layer. This process enhances both wear resistance and fatigue strength.
4.Ceramic Coatings
With their exceptional hardness and thermal resistance, ceramic coatings find applications in demanding environments. These coatings contribute significantly to the durability of plastic mold components.
5.Teflon and Other Polymer-Based Coatings
Polymer-based coatings, such as Teflon, offer unique advantages, including non-stick properties and corrosion resistance. These coatings are beneficial in specific molding applications.
Comparative Analysis
Evaluation of the Pros and Cons
As users explore surface coating options, it’s crucial to understand the strengths and limitations of each technology. PVD coatings, for instance, excel in hardness but may have cost considerations. While providing excellent wear resistance, DLC coatings might require specialized application processes.
Consideration of Industry-Specific Requirements
Different industries have unique demands for plastic mold components. The choice of surface coating should align with these requirements, ensuring optimal performance in specific applications.
Application Scenarios
Practical Examples
Understanding how surface coating technologies impact performance in real-world applications is crucial for users making informed decisions.
1.PVD Coatings in Action
Plastic mold components enhanced with PVD coatings perform remarkably in high-precision injection molding. The hardness of the coating ensures minimal wear, even in prolonged production cycles.
2.DLC-Coated Components in High-Friction Environments
In applications with elevated friction levels, such as molds for complex geometries, DLC-coated components demonstrate superior wear resistance, resulting in extended tool life.
3.Nitrided Moulds for Enhanced Fatigue Resistance
Nitriding processes prove advantageous when mold components are subjected to repetitive stress. The hardened surface significantly improves fatigue resistance, contributing to longer mold life.
4.Ceramic Coatings for Extreme Conditions
Industries dealing with high-temperature or corrosive materials benefit from ceramic coatings’ thermal and chemical resistance. Plastic mold components maintain their integrity even in harsh environments.
5.Polymer-Based Coatings for Specific Moulding Applications
Teflon and other polymer-based coatings find prominence in applications where a non-stick surface is crucial. These coatings prevent material adhesion, simplifying the molding process and reducing downtime for cleaning.
Factors to Consider When Choosing Surface Coatings
Material Compatibility
Users seeking plastic mold components must consider the compatibility of surface coatings with the base material. It ensures a seamless integration that maximizes the benefits of the layer.
Cost-Effectiveness and Long-Term Value
While certain coatings may have higher initial costs, evaluating long-term value is essential. Factors such as reduced maintenance expenses and extended tool life contribute to cost-effectiveness.
Maintenance Requirements and Ease of Cleaning
Understanding the maintenance needs of coated mold components is crucial for uninterrupted production. Coatings with accessible cleaning properties can significantly reduce downtime associated with maintenance.
Addressing Common User Concerns
Responding to User Queries
As users contemplate the integration of surface coatings into their plastic mold components, common concerns often arise. Addressing these queries helps users make informed decisions.
1.Precision Concerns
Users may wonder whether the application of coatings affects the precision of plastic mold components. In general, when applied correctly, modern coating technologies maintain or enhance accuracy, contributing to consistent and high-quality outputs.
2.Impact on Production Efficiency
Understanding how coatings influence production efficiency is crucial for users focused on optimizing their manufacturing processes. Well-chosen layers can reduce downtime, increase tool life, and improve efficiency.
Clarification on Coating Benefits
1.Reducing Downtime and Maintenance Costs
Highlighting the role of surface coatings in minimizing downtime and maintenance costs is paramount. Coated plastic mold components often require less frequent maintenance, increasing operational efficiency.
I
As environmental considerations become increasingly significant, the industry is witnessing a shift towards sustainable coating solutions. Manufacturers are exploring eco-friendly alternatives that maintain performance while minimizing environmental impact.
Conclusion
In enhancing plastic mold components’ wear resistance and longevity through advanced surface coatings, selecting the right supplier, connecting with a trusted company, and choosing a capable manufacturer are pivotal steps. Users can empower their operations with durable and high-performance plastic mold components by making informed choices at each stage.
Thank you for exploring the world of surface coating technologies for plastic mold components. Please let me know if you have any further questions or topics you’d like to delve into!