In the world of plastic injection molding, hot runner systems have become a preferred choice for manufacturers seeking enhanced efficiency, improved quality, and cost savings. As a hot runner system supplier, it is crucial to understand the significant advantages that these systems offer. In this article, we will explore the benefits of hot runner systems in plastic injection molding and their impact on the manufacturing process.
Understanding Hot Runner Systems
A hot runner system is an assembly of heated components that deliver molten plastic directly to the mold cavity in an injection molding machine, eliminating the need for a cold runner. The hot runner system includes a manifold, nozzles, heaters, and temperature controllers. The molten plastic flows through the hot runner channels to the mold, resulting in more precise and efficient injection molding.
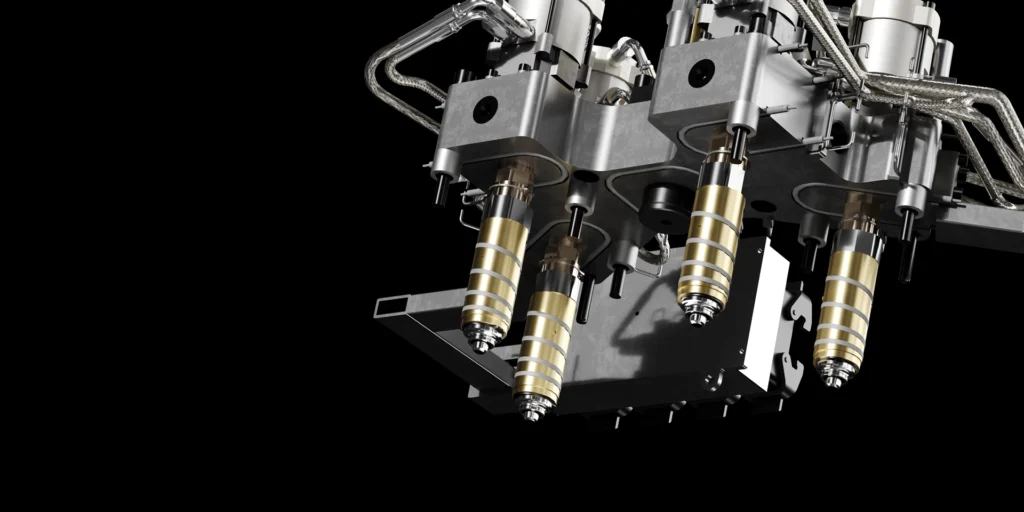
Advantages of Hot Runner Systems
1. Reduced Material Waste
Hot runner systems significantly reduce material waste compared to traditional cold runner systems. In cold runner systems, the excess plastic from the runner is discarded, leading to material loss. With hot runner systems, the plastic is contained within the heated channels and does not solidify, minimizing or eliminating the need for runners and reducing material waste. This advantage can result in substantial cost savings over time, especially for high-volume production.
2. Improved Cycle Time
Hot runner systems enable faster cycle times in plastic injection molding. By eliminating the need for the runner to solidify and cool down, the process becomes more efficient and faster. The molten plastic is delivered directly to the mold cavity, resulting in quicker fill times and reduced cooling times. This increased production speed translates to higher productivity and shorter lead times for manufacturers.
3. Enhanced Part Quality
Hot runner systems contribute to improved part quality and consistency. The precise temperature control in hot runner systems ensures uniform melt flow and reduces the risk of flow-related defects, such as warping, sink marks, or short shots. The elimination of cold runners also minimizes the occurrence of gate marks or vestiges, resulting in visually appealing and high-quality finished products.
4. Design Flexibility
Hot runner systems offer greater design flexibility in plastic injection molding. Manufacturers have more control over gate placement, allowing for more complex and intricate part designs. With hot runner systems, it is possible to achieve multi-cavity molds, family molds, or molds with multiple injection points, enabling the production of diverse part geometries and configurations.
5. Cost Savings
While the initial investment for hot runner systems may be higher than that of cold runner systems, they often result in long-term cost savings. The reduction in material waste, improved cycle times, and enhanced part quality contribute to overall cost savings in production. Manufacturers can achieve higher output, minimize scrap, and reduce the need for secondary operations, leading to improved profitability.
6. Process Control and Automation
Hot runner systems offer excellent process control and automation capabilities. The temperature controllers allow precise temperature regulation, ensuring consistent melt flow and optimal processing conditions. Advanced control systems and sensors monitor and adjust parameters, such as temperature and pressure, in real-time, optimizing the injection molding process and reducing the risk of defects or production issues.
Conclusion
As a hot runner system supplier, understanding the advantages that hot runner systems bring to plastic injection molding is crucial. The reduced material waste, improved cycle time, enhanced part quality, design flexibility, cost savings, and process control make hot runner systems a preferred choice for manufacturers seeking efficient and high-quality production. By incorporating hot runner systems into their injection molding processes, manufacturers can optimize production, increase productivity, and deliver superior plastic parts to meet customer demands.