Welcome to our blog post on precision injection molding! Whether you’re new to or already familiar with the concept, this comprehensive overview will provide valuable insights into this manufacturing process. Precision injection molding is a versatile technique for creating complex and highly accurate plastic parts. This article explores the various aspects of precision injection moulding, its benefits, applications and how to find reliable manufacturers to customise products.
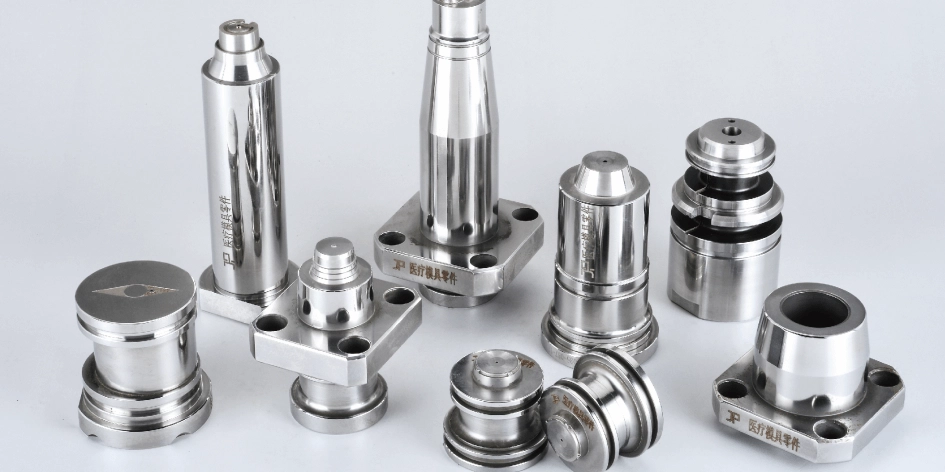
Introduction to Precision Injection Molding
Precision injection moulding is a manufacturing process that produces intricate plastic parts with exceptional accuracy. This involves the injection of a liquid plastic into a mould, allowing the plastic to cool and harden, and then ejecting the finished part. This technique enables the creation of complex geometries and intricate details that would be challenging or even impossible with other manufacturing methods.
The key to precision injection molding lies in the precision and efficiency of the injection molding machine. These machines are designed to accurately control the molten plastic’s temperature, pressure, and flow rate. With precise control, manufacturers can consistently produce high-quality parts with tight tolerances.
The Precision Injection Molding Process
1. Mold Preparation: The precision injection molding process begins with the design and fabrication of a mold. The mold gives a negative impression of the desired part and is typically made from steel or aluminum. It is carefully prepared to ensure the finished part’s proper venting, cooling, and ejection.
2. Material Selection: Once the mold is ready, the next step is to choose the appropriate plastic material for injection. Factors such as mechanical properties, chemical resistance, and cost are considered during the material selection.
3. Injection Phase: The selected plastic material is heated to its melting point and injected under high pressure into the mold cavity. The melted plastic fills the cavity, conforming to the mould and creating the intended component.
4. Cooling and Solidification: After injection, the mold is cooled to allow the molten plastic to solidify and take on the desired shape. Cooling time is carefully controlled to prevent warping or other defects in the finished part.
5. Ejection: The mold opens once the plastic has solidified and the finished part is ejected. The ejector pins or mechanisms built into the mold help push the part out while maintaining its integrity.
6. Post-Processing: Depending on the specific requirements of the part, post-processing steps such as trimming, deburring, or surface finishing may be necessary to achieve the desired final product.
Benefits of Precision Injection Molding
Precision injection molding offers a range of benefits, making it a widely used manufacturing process in various industries. Some key advantages include:
· Cost-effectiveness: Precision injection molding allows for efficient mass production of plastic parts, reducing manufacturing costs and enabling economies of scale.
· Design Flexibility: This technique offers exceptional design flexibility, allowing for complex geometries, intricate details, and the incorporation of multiple features into a single part. It opens up possibilities for innovative product designs that would be challenging with other manufacturing methods.
· Material Options: Precision injection molding supports a wide range of plastic materials, each with unique properties. Manufacturers can choose from various materials to meet specific requirements, such as strength, durability, chemical resistance, or transparency.
· Consistency and Accuracy: The precise control over the injection molding process ensures consistent parts production with tight tolerances. This results in high-quality products that meet strict specifications.
· Quick Turnaround Time: Once the mold is prepared, precision injection molding allows for rapid production cycles, enabling faster time-to-market for new products. The short manufacturing time means manufacturers can meet tight deadlines and respond quickly to market demands.
Applications of Precision Injection Molding
Precision injection molding finds applications in various industries due to its versatility and accuracy. Some common areas where this manufacturing process is widely employed include:
· Automotive Industry: Precision injection molded parts are extensively used in the automotive industry for interior and exterior components, under-the-hood parts, electrical connectors, and more. The ability to produce complex geometries and achieve tight tolerances makes it ideal for automotive applications.
· Electronics and Electrical Industries: The demand for precision-molded plastic parts is ever-growing in the electronics and electrical industries. These parts include connectors, housings, switches, and other components that require high accuracy, durability, and resistance to harsh environments.
· Medical and Healthcare Sector: Precision injection molding is crucial in the medical and healthcare sector, where precision and accuracy are paramount. Components such as syringes, medical device housings, surgical instruments, and drug delivery systems are commonly manufactured using this process.
· Consumer Products: Many products rely on precision injection molding for manufacturing. Items such as packaging containers, household appliances, toys, and various plastic parts benefit from the accuracy and repeatability of this process.
Choosing a Reliable Precision Injection Molding Manufacturer
Finding a reliable manufacturer is critical when it comes to customizing products using precision injection molding. Here are a few things to consider when choosing a manufacturer for your precision injection molding needs:
1. Expertise and Experience: Look for manufacturers with extensive experience in precision injection molding. They should have a proven track record of producing high-quality parts and serving diverse industries.
2. Quality Assurance: Ensure the manufacturer has robust quality control measures. They should follow strict quality standards and have certifications that validate their commitment to excellence.
3. Design and Engineering Support: A reliable manufacturer should have a team of skilled designers and engineers who can assist in product development, mold design, and optimization. Their expertise could assist with streamlining the manufacturing process and enhancing the final product’s quality.
4. Manufacturing Capabilities: Evaluate the manufacturer’s production capacity, equipment capabilities, and scalability. Ensure they meet your project’s requirements regarding quantities, lead times, and customization options.
5. Material Options: Check if the manufacturer offers a wide range of plastic materials suitable for precision injection molding. This ensures that you can select the best material for your specific application.
6. Customer Reviews and Testimonials: Research customer reviews and testimonials to gauge the manufacturer’s reputation, reliability, and customer satisfaction. This can provide valuable insights into their capabilities and service quality.
How to Customize Your Products with Precision Injection Molding
Customizing your products using precision injection molding involves the following steps:
1. Concept Development: Start by conceptualizing your product design, considering its intended function, aesthetics, and desired features. Collaborate with experienced designers and engineers to refine your ideas and ensure manufacturability.
2. Design and Prototyping: Once the concept is finalized, work with the manufacturer’s design team to create detailed 3D CAD models of your product. These models will be used to develop the mold and produce prototypes for testing and validation.
3. Mold Design and Fabrication: The manufacturer’s mold design and engineering team will translate the 3D CAD models into a mold design. The design will be optimized for production efficiency and part quality. After finalizing the design, the mold fabrication process begins.
4. Testing and Validation: The manufacturer will produce prototypes using the precision injection molding process once the mold is ready. These prototypes will undergo rigorous testing and validation to meet all functional and quality requirements.
5. Production and Customization: Upon final approval of the prototypes, production begins. The manufacturer will utilize the precision injection molding process to produce the desired quantity of customized parts, adhering to the agreed specifications and quality standards.
6. Post-Processing and Assembly: Depending on your product requirements, the manufacturer may perform post-processing steps such as trimming, deburring, or surface finishing. They can also assist with the assembly of various components, if necessary.
Conclusion
Precision injection molding is a versatile manufacturing process that offers exceptional accuracy, design flexibility, and cost-effectiveness. Its wide range of applications and numerous advantages have become an indispensable technique for customizing plastic parts in various industries. By choosing a reliable precision injection molding manufacturer and following the customization process, you can bring your innovative product ideas to life. So, whether you’re working on automotive components, electronics, medical devices, or consumer products, precision injection molding is a reliable solution to meet your manufacturing needs. Don’t hesitate to explore the exciting possibilities this advanced manufacturing process offers!