Introduction
In the intricate world of manufacturing, Stamped Mold Parts play a crucial role, serving diverse industries with their precision and efficiency. As users seek to enhance their production processes, the optimization of Stamped Mold Parts becomes a pivotal consideration. This article delves into the transformative role of computational modeling in achieving optimal results, addressing the needs of users who are in the market for top-quality Stamped Mold Parts.
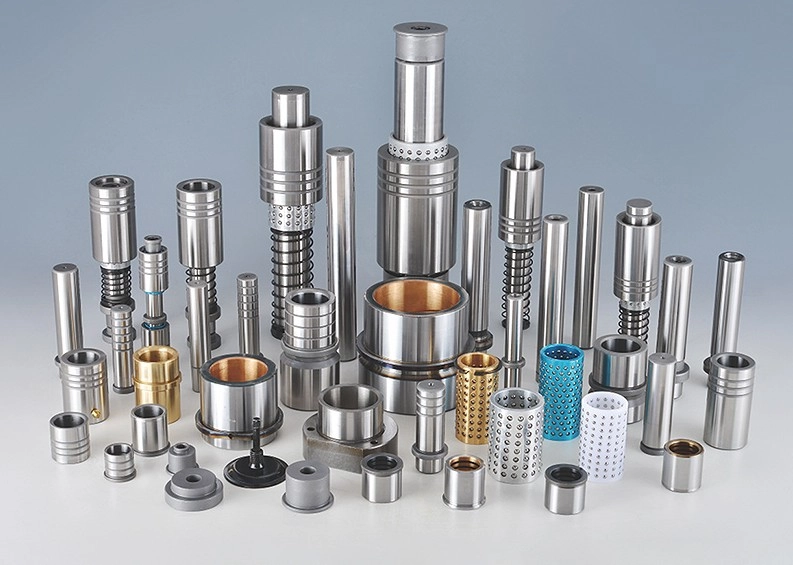
Understanding Stamped Mold Parts
Stamped Mold Parts are integral components in various manufacturing applications, ensuring the production of high-quality products. Industries such as automotive, aerospace, and electronics rely on the precision and reliability of these parts. Users looking to purchase Stamped Mold Parts must consider factors such as material quality, design specifications, and production efficiency.
Key Considerations for Users
When selecting a Stamped Mold Parts supplier, users need to focus on key considerations to ensure the desired outcomes. The manufacturing industry is dynamic, and staying ahead requires choosing suppliers who understand the nuances of CNC lathe processing, a technique commonly employed in the production of Stamped Mold Parts. The supplier’s expertise in CNC lathe processing directly influences the quality and precision of the final product.
This brings us to the critical role of computational modeling in optimizing Stamped Mold Parts.
Challenges in Stamped Mold Part Optimization
Stamped Mold Parts have their challenges in the manufacturing process. Identifying and addressing common issues, such as variations in material properties and geometric complexities, is vital. Precision and efficiency are paramount concerns for users seeking optimal Stamped Mold Parts.
To overcome these challenges, manufacturers have turned to advanced optimization techniques, with computational modeling emerging as a critical player in this domain. Computational modeling provides a dynamic approach to simulate and analyze various manufacturing scenarios, allowing for precise adjustments and improvements in the production process.
The Significance of Computational Modeling
Definition and Explanation
Computational modeling involves creating virtual representations of physical systems to simulate their behavior and performance. Applied to Stamped Mold Parts, this method allows manufacturers to analyze and optimize the production process before physically creating the parts.
Application to Stamped Mold Parts
In the context of Stamped Mold Parts, computational modeling enables manufacturers to simulate the entire manufacturing workflow. This includes the CNC lathe processing steps and the interactions between different components. By virtually testing and refining the process, manufacturers can identify potential issues and make informed decisions to enhance efficiency.
Advantages of Computational Modeling
The advantages of employing computational modeling for Stamped Mold Parts optimization are multifaceted. It offers a cost-effective means of experimentation, reduces the need for physical prototypes, and accelerates the product development cycle. Manufacturers can fine-tune parameters, assess the impact of design changes, and ultimately deliver high-quality Stamped Mold Parts.
Key Features of Computational Modeling
Simulation Capabilities
Computational modeling provides realistic simulations of the Stamped Mold Parts manufacturing process. This includes the behavior of materials, the impact of tooling, and the overall performance of the CNC lathe processing. Users can visualize the entire production cycle and make data-driven decisions based on accurate simulations.
Predictive Analysis
One of the strengths of computational modeling is its predictive analysis capabilities. Users can anticipate potential challenges in the Stamped Mold Parts production, allowing for proactive adjustments to enhance efficiency and precision. This foresight is invaluable in delivering optimal results.
Real-World Examples
Numerous success stories illustrate the effectiveness of computational modeling in Stamped Mold Parts optimization. Companies leveraging this technology have reported significant improvements in production efficiency, reduced costs, and enhanced product quality. These real-world examples showcase the practical benefits of incorporating computational modeling into the manufacturing process.
Addressing User Concerns
As users explore the realm of Stamped Mold Parts optimization through computational modeling, it’s essential to address common questions and concerns. Users often wonder about the reliability of virtual simulations, the applicability of results to real-world scenarios, and the overall impact on their specific manufacturing processes.
Common Questions and Doubts:
Reliability of Virtual Simulations: Users may question the accuracy of virtual simulations compared to physical testing. Addressing this concern involves highlighting the advancements in simulation technologies, ensuring that virtual models closely mirror real-world conditions.
Applicability of Results: Users want assurance that the insights gained from computational modeling are directly applicable to their CNC lathe processing and Stamped Mold Parts production. Emphasize the customization capabilities of modeling tools to align with specific manufacturing environments.
Integration into Existing Processes: How seamlessly can computational modeling integrate into their current production workflows? Clarify that modern modeling tools are designed for easy integration, providing a smooth transition without disrupting established processes.
Industry Trends and Innovations
The landscape of Stamped Mold Parts manufacturing is continuously evolving, with emerging technologies and industry trends shaping the future. Keeping abreast of these trends is crucial for users aiming to stay competitive and efficient in their operations.
Emerging Technologies:
Advanced Materials: Explore how computational modeling adapts to incorporate advancements in materials science, allowing users to optimize Stamped Mold Parts for durability, flexibility, and other desired properties.
IoT Integration: Discuss the potential integration of computational modeling with Internet of Things (IoT) devices for real-time monitoring and feedback, further enhancing the precision and efficiency of CNC lathe processing.
Industry Trends:
Automation and Robotics: Analyze how computational modeling aligns with the growing trend of automation and robotics in manufacturing. This synergy can lead to enhanced productivity and reduced production times for Stamped Mold Parts.
Sustainability Initiatives: Examine how manufacturers using computational modeling contribute to sustainability goals. This includes minimizing material waste, optimizing energy consumption, and adopting eco-friendly practices in Stamped Mold Parts production.
The Future of Optimization Through Computational Modeling
The trajectory of computational modeling in Stamped Mold Parts optimization points toward a future characterized by even greater accuracy, efficiency, and customization. Continuous advancements in simulation technologies, coupled with a deeper understanding of material science, are set to revolutionize the manufacturing landscape.
Choosing the Right Computational Modeling Approach
Selecting the appropriate computational modeling approach is a critical decision that significantly influences the success of Stamped Mold Parts optimization. Users must carefully consider several factors to ensure compatibility with their specific manufacturing requirements.
Considerations When Selecting a Computational Modeling Method:
Accuracy and Precision: Assess the modeling method’s accuracy in simulating CNC lathe processing and the production of Stamped Mold Parts. Look for validation through comparisons with physical prototypes and real-world results.
Adaptability: Consider the adaptability of the modeling approach to different Stamped Mold Parts designs and materials. The versatility to handle variations in manufacturing specifications is essential for comprehensive optimization.
Ease of Integration: Evaluate how seamlessly the chosen computational modeling method integrates into existing workflows. A user-friendly interface and compatibility with industry-standard software contribute to a smoother transition.
Compatibility with Stamped Mold Parts:
Material-Specific Modeling: Highlight the importance of computational modeling methods that accommodate various materials commonly used in Stamped Mold Parts. This includes metals, plastics, and composite materials, ensuring broad applicability.
Precision in CNC Lathe Processing: Emphasize the modeling approach’s ability to simulate the intricacies of CNC lathe processing accurately. This involves capturing toolpath dynamics, material removal rates, and potential challenges unique to Stamped Mold Parts production.
Cost-Benefit Analysis for Users:
Investment vs. Returns: Provide insights into the initial investment required for implementing computational modeling and how it correlates with long-term returns. Illustrate potential cost savings, reduced production times, and improved product quality.
Training and Support: Discuss the training and support mechanisms offered by the computational modeling provider. User education is crucial for maximizing the benefits of the chosen approach in Stamped Mold Parts optimization.
Case Studies and Success Stories
To reinforce the practical advantages of computational modeling in the realm of Stamped Mold Parts, let’s delve into real-world examples of successful implementations.
Example 1: Streamlining CNC Lathe Processing
Company X, a leading Stamped Mold Parts manufacturer, integrated computational modeling into their production process. By simulating CNC lathe processing, they identified optimal toolpaths, reducing machining times by 15% and enhancing overall efficiency.
Example 2: Material Optimization for Durability
Company Y utilized computational modeling to analyze different material compositions for Stamped Mold Parts. The result was a material selection that improved part durability by 20%, leading to increased product lifespan and customer satisfaction.
Example 3: Cost-Effective Design Adjustments
Company Z implemented computational modeling to assess design modifications before physical prototyping. This iterative approach saved significant costs in tooling and materials, ensuring cost-effective Stamped Mold Parts production.
Conclusion
In the ever-evolving landscape of manufacturing, the optimization of Stamped Mold Parts stands as a critical determinant of success. As users navigate the complexities of CNC lathe processing and material intricacies, the integration of computational modeling emerges as a transformative solution. This article has explored the multifaceted role of computational modeling in achieving optimal results, addressing the concerns and considerations of users in search of top-quality Stamped Mold Parts.
Key Takeaways:
Precision Through Simulation: Computational modeling provides a dynamic platform to simulate and analyze the entire Stamped Mold Parts production process. Users gain unprecedented precision through virtual experimentation, leading to enhanced product quality.
Versatility in Material and Design: The adaptability of computational modeling to various materials and design specifications empowers users to tailor the optimization process to their unique manufacturing requirements. This versatility ensures comprehensive solutions for Stamped Mold Parts.
Realizing Cost-Effective Solutions: Through case studies and success stories, we’ve witnessed how computational modeling contributes to cost-effective solutions. Whether streamlining CNC lathe processing or optimizing material selection, users can achieve tangible cost savings.
A Glimpse into the Future: Industry trends and innovations indicate a promising future for Stamped Mold Parts optimization through computational modeling. Advancements in technology, coupled with sustainability initiatives, position this approach as a driving force in manufacturing evolution.
As users contemplate the integration of computational modeling into their Stamped Mold Parts production, the emphasis should be on selecting the right approach that aligns with their specific needs. A careful evaluation of modeling methods, consideration of compatibility, and a thorough cost-benefit analysis are crucial steps in this journey.
In conclusion, the journey towards optimized Stamped Mold Parts is not just a technological leap but a strategic investment in the future of manufacturing. Computational modeling, when harnessed effectively, propels users into a realm of precision, efficiency, and innovation, ensuring their place at the forefront of the dynamic manufacturing landscape.
Choose wisely, optimize confidently, and usher in a new era of excellence in Stamped Mold Parts production.