Introduction
Die-casting mold parts play a pivotal role in modern manufacturing processes, influencing the quality and efficiency of production. For prospective buyers seeking to enhance the performance of their operations, a critical consideration lies in the judicious selection of materials and coatings. This article explores the impact of advanced materials and coatings on optimizing the performance of die-casting mold parts.
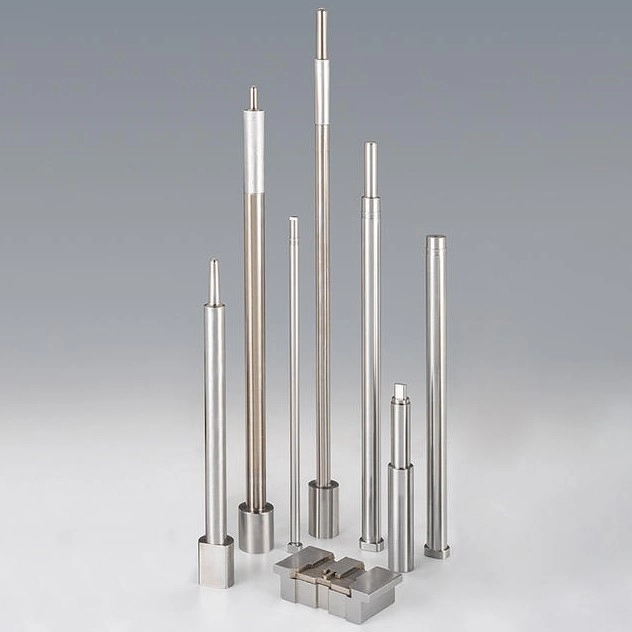
Fundamentals of Die Casting Mold Parts
Die-casting mold parts, comprising intricate components, are integral to producing precise and high-quality goods. The selection of materials for these parts is a crucial determinant of their overall performance. Users face challenges in achieving the desired efficiency due to various factors, making exploring advanced solutions imperative.
The Impact of Advanced Materials
Using advanced materials has become a game-changer in the realm of die-casting mold parts. These materials, characterized by enhanced durability, superior heat resistance, and heightened precision, contribute significantly to performance optimization. Die-casting mold parts suppliers increasingly incorporate these advanced materials into their offerings, providing users with solutions that meet and exceed industry standards.
Coatings for Performance Enhancement
While advanced materials set a robust foundation for die-casting mold parts, coatings enhance performance. Coatings act as protective layers, improving resistance to wear, corrosion, and temperature fluctuations. In the die-casting mold parts industry, choosing coatings is as crucial as selecting materials.
Die-casting mold parts suppliers recognize the significance of coatings in extending the lifespan and improving the efficiency of their products. Collaboration between advanced materials and specialized coatings is a crucial strategy leading suppliers and factories employ to deliver high-performance die-casting mold parts.
Considerations for Material and Coating Selection
As buyers navigate the landscape of die-casting mold parts, understanding the material and coating selection considerations is paramount. Here are key factors influencing the decision-making process:
Factors Influencing Material Selection
The choice of material for die-casting mold parts hinges on various factors, including:
1.Mechanical Properties
Strength: Ensuring the material can withstand the forces involved in the die-casting process.
Hardness: Resisting wear and tear over the lifecycle of the mold.
2.Thermal Conductivity
Heat Resistance: Maintaining structural integrity at elevated temperatures.
Thermal Conductivity: Facilitating uniform heat distribution during casting.
3.Machinability
Ease of Machining: Simplifying the manufacturing process for intricate mold components.
Surface Finish: Achieving the desired level of smoothness for the molded products.
In die-casting mold parts, leading suppliers and factories consider these factors to provide materials that align with diverse user requirements.
Compatibility of Coatings with Different Materials
In optimizing die-casting mold parts performance, the synergy between coatings and materials is critical. Layers are not universal; their effectiveness depends on the compatibility with specific materials. Here’s a closer look at this crucial interplay:
Matching Coating Properties with Material Characteristics
1.Adhesion
Ensuring the coating securely bonds with the chosen material, preventing delamination.
2.Chemical Compatibility
Verifying that the coating is resistant to chemicals involved in the die-casting process.
3.Thermal Expansion
Aligning the coefficient of thermal expansion between the layer and material to avoid cracks and distortion.
Tailoring Coatings to Performance Requirements
1.Wear Resistance
Selecting coatings with high wear resistance for prolonged mold life.
2.Release Properties
Choosing layers that facilitate easy demolding of the final product.
3.Corrosion Resistance
Implementing coatings that protect against corrosion in harsh operating environments.
Leading die-casting mold parts suppliers understand the nuanced relationship between coatings and materials, offering tailored solutions that address the specific needs of diverse industries.
Real-world Applications and Success Stories
Applying advanced materials and coatings in die-casting mold parts has yielded remarkable success stories across various industries. Here, we highlight instances where the strategic selection of materials and coatings has led to tangible improvements:
Automotive Industry Advancements
Die-casting mold parts in the automotive sector demand precision and durability. Suppliers integrating advanced materials with specialized coatings have witnessed the following:
Extended Tool Life: Advanced materials combined with wear-resistant coatings result in longer-lasting molds.
Improved Surface Finish: Coatings enhance the appearance and quality of automotive components.
Aerospace Sector Innovations
In aerospace applications, where stringent standards prevail, the utilization of advanced materials and coatings has resulted in:
Enhanced Thermal Stability: Materials with superior heat resistance and thermal barrier coatings.
Optimized Component Tolerance: Coatings facilitating precise casting for intricate aerospace parts.
Electronics Manufacturing Excellence
Die-casting mold parts play a crucial role in electronics manufacturing. The adoption of advanced materials and coatings has led to:
Increased Productivity: Reduced downtime due to improved wear resistance.
Consistent Product Quality: Coatings ensure uniformity in molded electronic components.
Leading die-casting mold parts factories and suppliers continually innovate, pushing the boundaries of what is achievable with advanced materials and coatings. These success stories underscore the practical benefits for users seeking optimal performance in their manufacturing processes.
Future Trends and Innovations in Die Casting Mold Parts
The die-casting mold parts industry is poised for transformative changes as technology advances. Here, we delve into emerging trends and innovations that will shape the future landscape:
Integration of Smart Technologies
1.Sensor Integration
Embedding sensors in die-casting molds for real-time temperature, pressure, and wear monitoring.
Enhancing predictive maintenance strategies for improved mold longevity.
2.Industry 4.0 Connectivity
Incorporating die-casting mold parts into interconnected systems for seamless data exchange.
Enabling remote monitoring and control for heightened operational efficiency.
Sustainable Material Development
1.Biodegradable Materials
Exploring materials that offer durability while being environmentally friendly.
Addressing the growing demand for sustainable manufacturing practices.
2.Recyclable Coatings
Developing coatings with recyclability in mind to reduce environmental impact.
Meeting the increasing focus on circular economy principles.
Advanced Simulation and Modeling
1.Virtual Prototyping
Utilizing advanced simulation tools for comprehensive virtual testing of die-casting mold designs.
Reducing the need for physical prototypes and accelerating the development process.
Conclusion
The future of die-casting mold parts lies at the intersection of advanced materials, intelligent technologies, and sustainable practices. Industry players, including die-casting mold parts suppliers and factories, must stay abreast of these trends to remain competitive and meet the evolving needs of users.
In this comprehensive exploration, we’ve covered the current impact of advanced materials and coatings, material and coating selection considerations, real-world success stories, and future trends. Armed with this knowledge, buyers can make informed decisions to optimize the performance of their die-casting mold parts.
For more information or to explore the latest die casting mold parts innovations, connect with your trusted Die Casting Mold Parts supplier.